Fragmentos de la Industria 4.0: SENSORES IO LINK
Durante las últimas semanas se ha desarrollado con más fuerza la noticia de la llegada de la industria 5.0, pero espera que? Si muchos de nosotros apenas y entendemos la industria 4.0 o no? Si es así, entonces debemos de poco a poco terminar de recabar a profundidad y entender los principios de la industria 4.0. Dentro de los fragmentos de esta industria el estándar de redes de comunicaciones industriales IO Link juega un papel sumamente importante. Esta comunicación digital de punto a punto y de corta distancia que permite conectar sensores y actuadores digitales a diferentes tipos de bus, especialmente a buses de campo industrial o a Ethernet industrial. Este estándar internacional está representado por la norma IEC 61131-9, además que permite un diagnóstico y localización de errores centralizado a un nivel de sensores – actuadores [1]. A medida que la innovación en tecnologías referentes a la industria crece es importante conocer la tecnología utilizada desde el sensor / actuador de campo hasta el sistema de software integral y dinámico (MES) que se encarga de realizar un respectivo monitoreo, rastrear, documentar y controlar el proceso de fabricación desde la materia prima hasta el producto terminado como tal. Por tanto, el estándar IO Link forma una parte esencial en el ámbito de la pirámide de la automatización en términos de la industria 4.0.
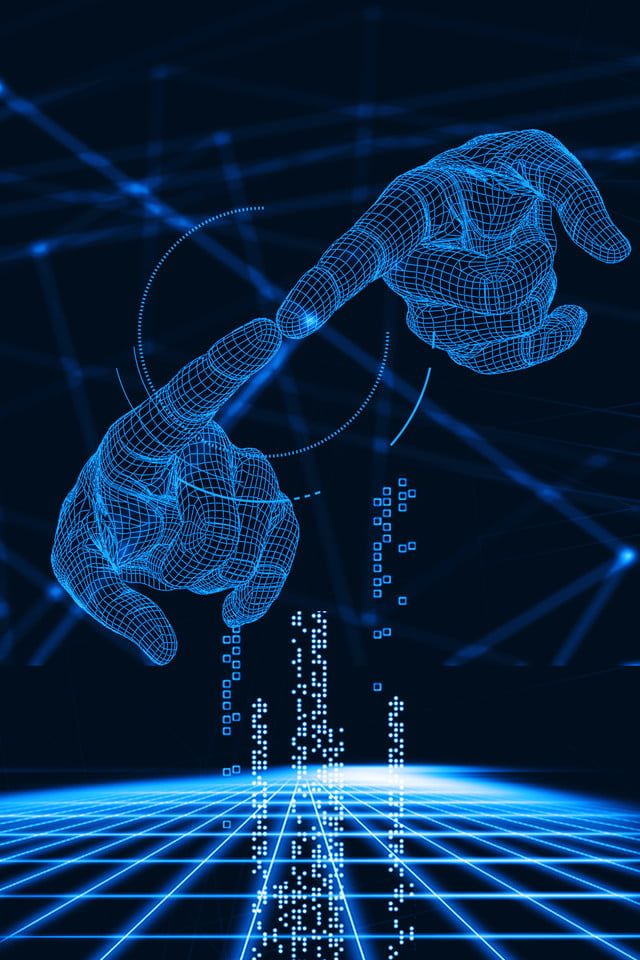
Siendo así entonces IO-link representa una conexión punto a punto, y es importante no confundir esto con un bus de campo, ya que, esta conexión de punto a punto se realiza a través de un sensor con funcionalidades IO-link hacia un master como un PLC. Esta comunicación es bidireccional debido a un protocolo serie que permite intercambiar paquetes de datos normalizados [2]. De esta manera un conjunto de varios sensores con características IO-Link se conectan hacia una central, la cual se conecta directo a un controlador (master) como un PLC, microcontrolador, etc. Los parámetros de configuración de cada sensor se transmiten de forma remota desde la central hacia el sensor y entonces, los datos medidos e información recolectada por el sensor se envía desde el mismo hacia la central, por tal esta comunicación es bidireccional.
Su conexión es bastante simple e intuitiva en el sector industrial. Generalmente para la alimentación de estos sensores se lo realiza mediante un cable de 3 hilos dado que este tipo de conexión viene desde un estándar específico para las instalaciones de campo. Como se muestra en la figura 2, se tiene la conexión de un sensor IO-Link que puede ser de 3 a 5 hilos. Así la alimentación del sensor se la realiza en los pines 1 y 3, y la transmisión de la señal es mediante el pin 4. Para establecer la comunicación entre el sensor y el controlador (master), el controlador debe enviar un llamado de “wake up” hacia el sensor para “despertarlo” y obtener la comunicación deseada
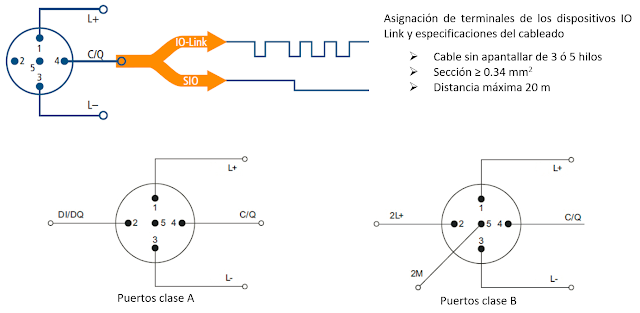
Varias marcas reconocidas dentro la automatización industrial tales como Omron, Siemens, Rockwell automation, IFM, Sick, Schneider electric, etc, cuentan dentro de sus catálogos tanto de sensores como actuadores, con características IO-Link. Como ejemplo, se tiene el caso de la reconocida marca IFM la cual dentro de sus catálogos cuenta con una amplia variedad de maestros y módulos IO-Link, sensores e identificación, indicación, evaluación y conexión tanto de equipos como accesorios y sistemas de conexión IO-Link. También cuenta con lo necesario para la parametrización como software IO-Link y kits de inicio en esta tecnología.
Así en términos de la misma marca de IFM se reconoce que las conexiones a través del protocolo de comunicación IO-Link se puede transmitir de manera confiable y en un formato exclusivo para señales digitales de conmutación de sensores binarios, valores de proceso de sensores analógicos y sus parámetros que se basan en una señal de 24V, evitando de esta forma errores en los valores de medición cuando sucede la transmisión y conversión de señales analógicas [4].
Recalcando entonces la definición y funcionamiento de los sensores y actuadores IO-Link, es bueno reconocer las ventajas que estos conllevan dentro de los procesos industriales, como, por ejemplo:
- La sustitución sencilla del dispositivo. Esto previene ajustes erróneos a través de una parametrización automática. Además, que esto ayuda a disminuir paros no planeados y la intervención constante de equipo técnico especializado [5]. Para comprender a los dispositivos IO-Link los cuales son bastante intuitivos no se necesita contar con personal específicamente capacitado en el tema.
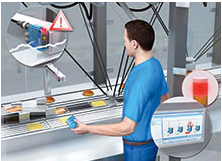
- Configuración flexible del sensor. Esta característica permite configurar los dispositivos IO-Link en función de distintas recetas que se necesiten utilizar en producción. Esta configuración de los dispositivos resulta ser también intuitiva y de fácil acceso al usuario (técnico u operario).
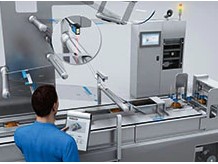
- Diagnostico de los dispositivos. Una de las características de IO-Link es que sus dispositivos pueden clasificase como “Smart” ya que realizan un constante monitoreo de condición de los mismos. De esta manera se tiene una optimización en cuestión de mantenimiento y los intervalos para los mismos, es decir, gracias a su monitoreo nos acercamos a lo que seria un mantenimiento predictivo y preventivo. Así entonces se tendrán menos riesgos de falla ya que tras un soporte técnico en cuestión de mantenimiento preventivo se realiza la detección y corrección de estados críticos de los dispositivos antes de que ocurra alguna falla.
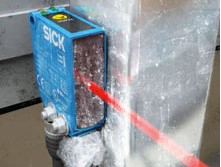
- Visualización y parametrización del sensor. De manera que se mencionó en primera instancia una característica particular de los sensores y actuadores IO-Link es que son “Smart” lo que permite tener la posibilidad de diagnosticar el estado del dispositivo. Para ello se puede contar con un software visualización el mismo que también permite la parametrización de funciones avanzadas del dispositivo.

- Transmisión y transformación de señales. Si se tiene un sensor que entrega medidas analógicas, al conectarlo directamente hacia un puerto IO-Link, este puede realizar la transformación de la señal analógica hacia una señal digital y a su vez, transmitir esta señal hacia el controlador.
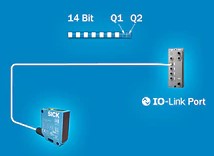
Tras recalcar las ventajas más importantes de los dispositivos estándares tipo IO-Link, dentro de la industria se tiene varios casos de éxito al implementar comunicación y dispositivos IO-Link en la automatización de sus procesos. Por esta y varias razones más a esta tecnología se la ha apodado con el nombre de “el USB de la automatización industrial”. Esto debido a que básicamente su funcionalidad es totalmente plug & play, así se tiene varias posibilidades ilimitadas dentro del control de aplicaciones industriales [6].
Referencias
[1] | Bihl Wiedemann, «¿Qué es IO-Link?,» Bihl+Wiedemann GmbH, Terrassa, 2023. |
[2] | X. Nolla, «¿Cómo funciona IO-link?,» WIKA, Sabadell, 2023. |
[3] | R. AS, «IO Link, el futuro inmediato de los sensores industriales,» 2019. |
[4] | IFM, «IO-LINK,» 2023. |
[5] | SICK, «IO-Link: ventajas de las funciones estándar,» Santiago de Chile, 2023. |
[6] | QuimiNet, «QuimiNet. Implementación de IO-Link en procesos de manufactura,» 20 Octubre 2017. [En línea]. Available: https://www.quiminet.com/articulos/implementacion-de-io-link-en-procesos-de-manufactura-4284556.htm. [Último acceso: 30 Marzo 2023]. |